Occupational Safety and Health Management
TIPC is committed to enhancing the performance of occupational safety and health management besides promoting workplace safety and health. We uphold the values of caring for our employees, contractors, port operators, and implementing occupational safety and health measures. We work hard to prevent occupational accidents and strive to provide a safe and healthy working environment for our employees and stakeholders. We foster a culture of safety and health where everyone is involved and actively promotes a "safe and healthy" friendly workplace culture. Our ultimate goal is to achieve zero occupational accidents and establish an excellent international corporate image in terms of workplace safety and health. To achieve this goal, TIPC has implemented and continues to uphold an occupational safety and health policy.
Occupational Safety and Health Policy
- Compliance with occupational safety and health regulatory requirements Promoting Workplace Safety and Health
- Implement risk assessment and management Enhance safety awareness and knowledge
- Improve the performance of occupational safety and health management Ensure worker consultation and participation
- Fulfillment of corporate social responsibility Continuous improvement and system optimization
Occupational Safety and Health Committee
To ensure the effective implementation of the occupational safety and health management system and achieve organizational effectiveness, communication channels are established between units to reach a consensus on occupational safety and health management. This allows for the commitment of employees or their representatives and external stakeholders to be established, along with effective two-way communication cannels. According to Article 23 of the Occupational Safety and Health Act, Article 10 of the Occupational Safety and Health Management Regulations, and the Regulations for the Establishment of the Occupational Safety and Health Committee of TIPC, the company has established the Occupational Safety and Health Committee which consist of 21 members, with 7 representing labor (one-third of all committee members). The chief executive officer (general manager) convenes meetings regularly every 3 months, where suggestions are made regarding the company's occupational safety and health policies. The committee also coordinates, recommends, reviews, and evaluates the company's compliance with statutory occupational safety and health management matters. Through this mechanism, the company ensures that its occupational safety and health management operations comply with regulatory requirements and continuously improves and enhances its management standards.
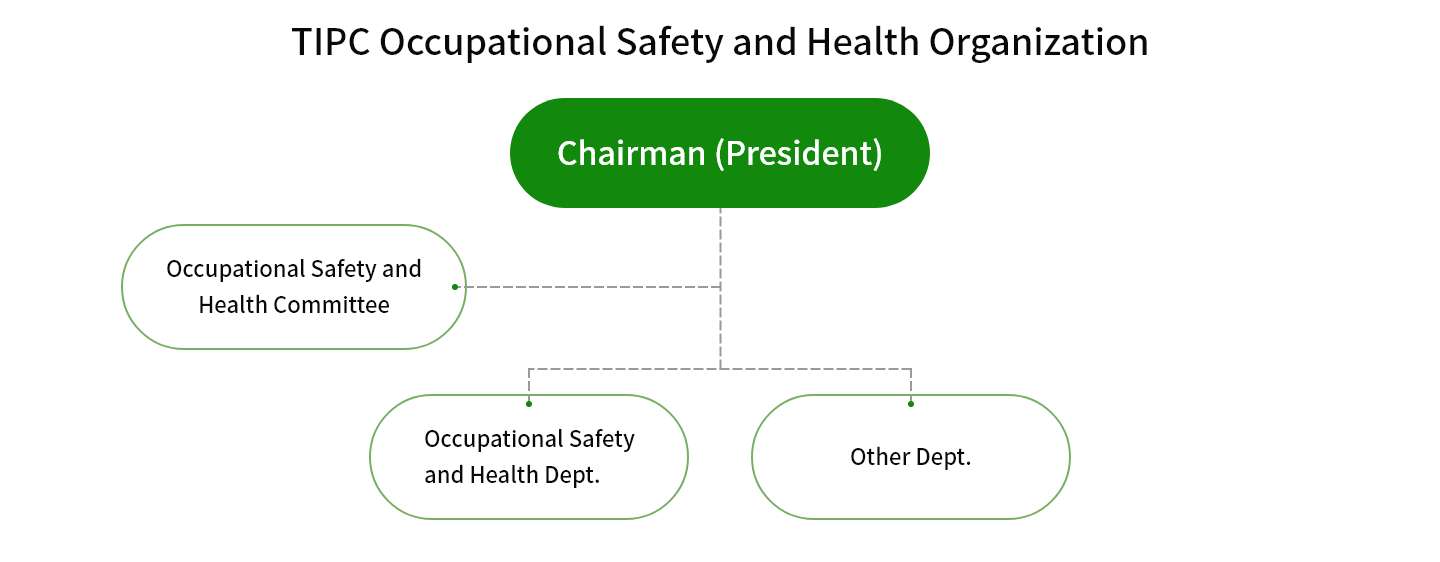
TIPC Occupational Safety and Health Organization
Occupational Safety and Health Management System
The formulation of the procedures and contents of the occupational safety and health management system in TIPC is based on the occupational safety and health policy of the Company, with reference to the principles of ISO/CNS 45001 standard, and further developed based on actual operational procedures. The occupational safety and health management system of the company covers a total of 2,116 employees, accounting for 100% of the workforce. The number of contracted vendors is approximately 608, accounting for about 34.8% of the employee workforce, subject to changes based on the execution of labor contracts.To stay updated on the trends of occupational safety and health regulations and address occupational safety and health issues and requirements from stakeholders, TIPC implements a regulatory compliance management procedure as part of its occupational safety and health management system, ensuring that the company's operations fully comply with the basic requirements of regulations.
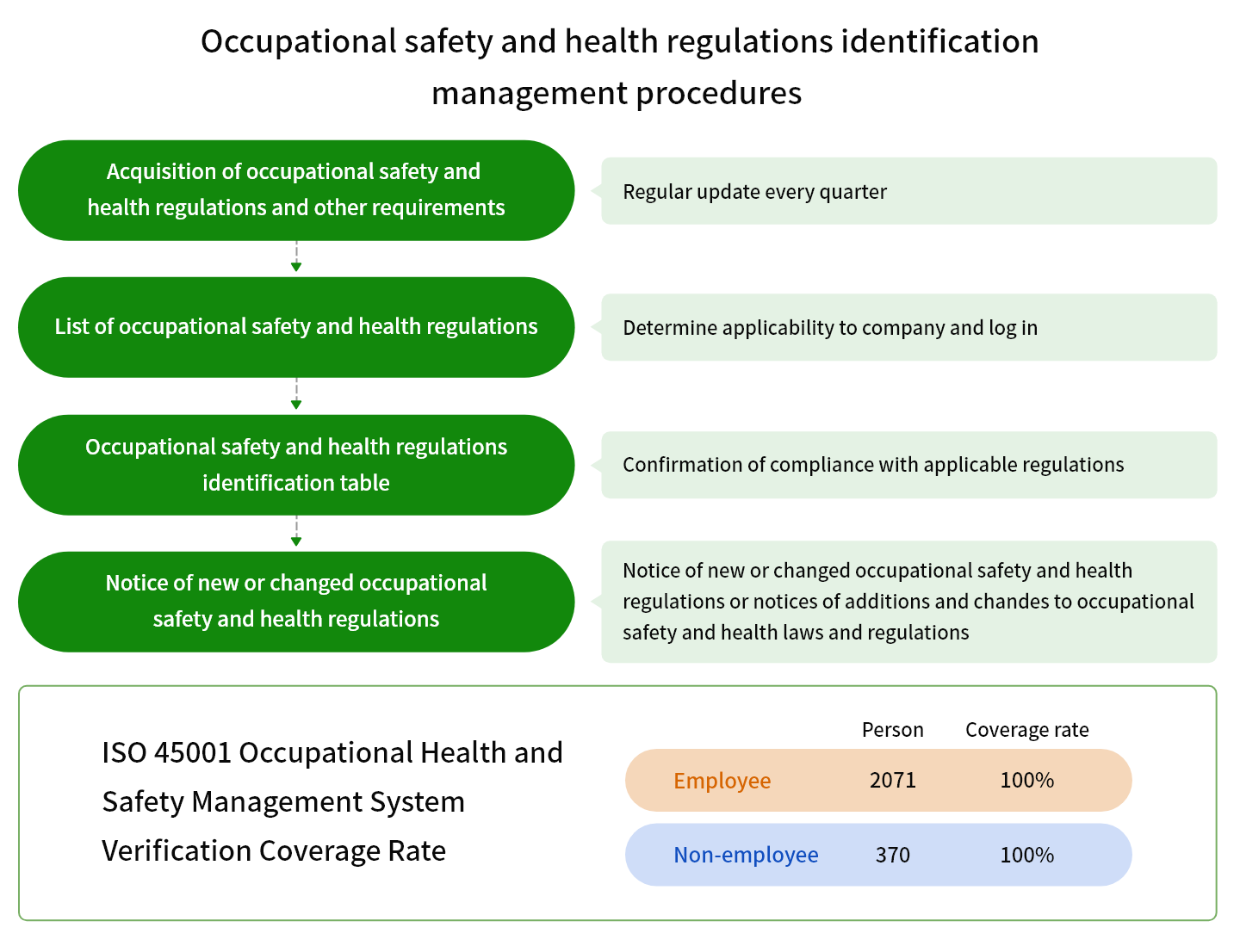
Occupational Safety and Health Management System
ISO 45001 Occupational Health and Safety Management System Verification Coverage Rate
Person | Coverage rate | |
---|---|---|
Employee | 2071 | 100% |
Non-employee | 370 | 100% |
TIPC has implemented the ISO 45001 Occupational Health and Safety Management System to enhance awareness and importance of safety and health among all levels of employees. By the end of May 2022, all divisions of the company (headquarters and branches in Keelung, Taichung, Kaohsiung, and Hualien) have successfully passed the ISO 45001/TOSHMS dual-system verification (certificate valid from June 12, 2022, to June 11, 2025). Furthermore, in May 2023, all divisions successfully passed the BSI surveillance audit. This demonstrates the company's firm commitment to workplace safety and health, highlighting its ongoing dedication to safety culture.
.jpg)
TIPC ISO/CNS 45001:ISO45001(2018) and TOSHMS certification
.jpg)
TIPC ISO/CNS 45001:ISO45001(2018) and TOSHMS certification
.jpg)
TIPC ISO/CNS 45001:ISO45001(2018) and BSI surveillance audit
E-management Platform Assisting Occupational Safety Management Work
TIPC utilized the cloud-based software tools for data integration and statistical functions, and providing real-time records of occupational safety inspection results and integration of ISO/CNS 45001 Occupational Safety and Health Management System Documents. Through the use of electronic tools for management and visualization charts, it enables monitoring of the Company's occupational safety and health management performance, enhancing operational efficiency and ensuring proactive management. Electronization projects
and functionalities include:
- Regulation Identification: Intelligent filtering of regulations, notification of updates, and data analysis for task assignment.
- Hazard Identification and Risk Assessment: Task assignment and data analysis.
- Inspection and Visits: Support for mobile devices, task assignment, and data analysis.
- Composite Indicators: Integration of the three important statistical tables or charts and display on a unified interface.
.jpg)
Workplace Safety
Through the Hazard Identification and Risk Assessment Procedure of the ISO 45001 Occupational Health and Safety Management System, the company identifies hazards and assesses risks for critical or high-risk tasks. Annually, prior to the management review meeting, all hazards and risk assessments within the company are periodically reviewed and confirmed. Additionally, periodic re-identification of hazards is conducted for relevant operational activities. When necessary, updates are made to serve as the basis for annual objectives and management plans, aiming to continuously improve the safety and health management system. Necessary control measures are implemented to keep risks at a tolerable level and enhance occupational safety and health performance, ultimately striving for zero accidents and ensuring employee workplace safety and health.
In order to establish a robust system for reporting and responding to major disasters and incidents, as well as to ensure that relevant units can promptly report and contact the necessary parties in the event of a major occupational accident involving port facilities, personnel, or ongoing construction projects (including sporadic projects), the Guidelines for Reporting and Responding to Major Occupational Disasters have been established. These guidelines provide a framework for reporting, emergency response, handling, and subsequent investigation and review to mitigate the impact of major occupational accidents, facilitate the swift restoration of normal workplace operations, and minimize loss. To control and achieve disaster reduction and mitigation, TIPC is implementing the following occupational safety and health management initiatives:
- Utilizing VR (Virtual Reality) technology for sensory education and training in occupational safety and health. This allows individuals to experience the risks and hazards associated with unsafe environments or behaviors, thereby enhancing training impressions and increasing safety awareness.
- Developing the occupational safety and health management plan for the year 2022, maintaining safety and health management goals/programs, and implementing measures to achieve occupational safety and health performance control for the company's employees and contractors.
- Conducting occupational safety and health supervision and audits in TIPC and utilizing electronic occupational safety and health cloud systems for data analysis to identify high-risk occupational safety and health issues.
- Unannounced inspections of high-risk operations on a quarterly basis.
- Supervising the subsidiary branches' implementation of Guidance on Safety and Health Management for Loading and Unloading at Harbor Terminals.
- Establishing a project team for occupational safety and health supervision in ongoing construction projects. This team supervises the safety of construction sites and loading/unloading operations at various subsidiary branches, strengthening the occupational safety and health units and the responsible parties for ongoing construction projects. They ensure that construction contractors comply with contractual requirements and are monitored by auditing and supervisory units to prevent occupational accidents.
- Implementing an occupational disaster prevention plan to effectively reduce operational hazards. This plan includes five execution programs: risk assessment and control, safety education and promotion, self-management capabilities, construction safety control, and performance evaluation. It aims to ensure occupational safety and health practices in the Company's units and to supervise contractors' construction safety and health management operations, while enhancing various measures for occupational accident prevention.
- Using the PDCA (Plan-Do-Check-Act) management cycle mechanism of the occupational safety and health management system to identify potential hazards in the working environment. Through continuous improvement, risks are reduced to an acceptable level and compliance with relevant regulations is achieved, ultimately enhancing safety and health management performance.
Furthermore, hazard identification and risk assessment are conducted for the work environment, and operational environment monitoring is implemented for hazardous operations to ensure the safety of contractor operations. Additionally, the Guidance on Safety and Health Management for Loading and Unloading at Harbor Terminals has been established to ensure the safety of terminal operations and prevent safety-related hazards in port operations.
To prevent any accidents from occurring, random and unannounced coaching visits are conducted for high-risk terminals or those that have experienced accidents during loading and unloading operations to check the safety and health self management of the operations. Additionally, participation in joint coaching visits organized by the Maritime Port Bereau or local branches is periodic. Furthermore, each month, the local branch reports on the implementation of safety and health management in the inspected port terminals, and continuous rolling reviews and controls are conducted.
Occupational Injury Statistics
Employee Occupational Injuries Statistics in 2023 | |||
---|---|---|---|
Total working hours | Total female working hours | 1,708,706 | |
Total male working hours | 2,465,596 | ||
Total working hours | 4,174,302 | ||
Number of recordable occupational injuries (including fatalities and serious occupational injuries) | Total occupational injuries (times) for females | 0 | |
Total occupational injuries (times) for males | 1 | ||
Total occupational injuries (times) | 1 | ||
Death rate from occupational injuries (%) | 0 | ||
Rate of severe occupational injuries (%) | 0 | ||
Recordable occupational injury rate (%) | 0.24 |
Notes.:
- Death rate from occupational injuries = (number of deaths due to occupational injuries/total working hours) *1,000,000.
- Rate of severe occupational injuries = [Number of severe occupational injuries (excluding fatalities)/Total working hours] *1,000,000.
- Recordable occupational injury rate = [Number of recordable occupational injuries (including fatalities and serious occupational injuries)/Total working hours] *1,000,000.
- Serious occupational injuries refer to occupational injuries that cannot be restored to a healthy state within 6 months.
- Recordable occupational injuries do not include occupational injuries caused by commuting to and from work.
- The employee was hit by a forklift truck, and the labor inspection unit was fined NT$120,000 for this case. When a colleague of our branch office was checking the position of goods at the sea side wall of the warehouse, he was hit by an empty truck forklift that was about to enter the warehouse for turning. The company's improvement measures are as follows: promote precautionary measures to staff, implement wearing of personal protective equipment, trial run on use of infrared-sensitive voice players for reminders at workplaces, remind staff to wear personal protective equipment while entering the workplace, improve port operation site marking, enhance hazard notification and education training for employees in the port area, etc.
Occupational Safety and Health Training
To enhance the proficiency of TIPC personnel in the Occupational Safety and Health Management System, training and education needs from various units are planned and consolidated according to the current situation and requirements. An annual training plan is implemented, with a focus on relevant units and colleagues within the company. When necessary, consideration is given to stakeholders such as port authorities, private enterprises, external stakeholders, and contractors. This includes both in-house training and external training, with sessions conducted by professional instructors. The company conducts general occupational safety and health education training for new employees in accordance with the Occupational Safety and Health Education and Training Regulations, achieving a coverage rate of 100% in 2023. For more information on occupational safety and healthrelated training in 2023, please refer to Appendix Three: Friendly Interaction Information.
Occupational Safety and Health Training
Occupational Safety and Health Training Statistics | ||
---|---|---|
Training program | Training program Number of trainees | Training fee (NT$) |
General safety and health education training (New/working employees, supervisors, OSHC members, work-study/interns) | 286 | 150,500 |
Safety and health promotion for loading and unloading operators and contractors | 403 | 51,500 |
On-the-job education and training for dangerous machine operators and hangers | 43 | 24,000 |
On-the-job education and training for forklift operators | 25 | 12,000 |
Occupational safety and health construction risk assessment and risk management | 31 | 18,000 |
CPR+AED training | 735 | 82.100 |
Training Type | Specific Training Plan |
---|---|
Internal training | General or specific occupational safety and health education/training, health seminars, internal audits training for occupational safety and health, regulatory identification training, hazard identification and risk assessment training, and occupational safety and health education/training for relevant personnel involved in related operations. |
External Training | Depending on the requirements of the supervisory authority or the business needs of each unit. |
.jpg)
On-the-job training for employees
.jpg)
New employee orientation and training
Employee Health Management
To implement the workplace health policy for its employees, the company has established the Employee Health Management Procedure and Employee Health Service Plan. Each year, funds are allocated for health check-ups, which are provided to employees free of charge. The scope and frequency of these checkups exceed current legal requirements, demonstrating the company's commitment to caring for employee health. Additionally, a Health Management Service Center is established, staffed with nurses specializing in occupational health services, offering employees timely access to professional health advice and assistance.
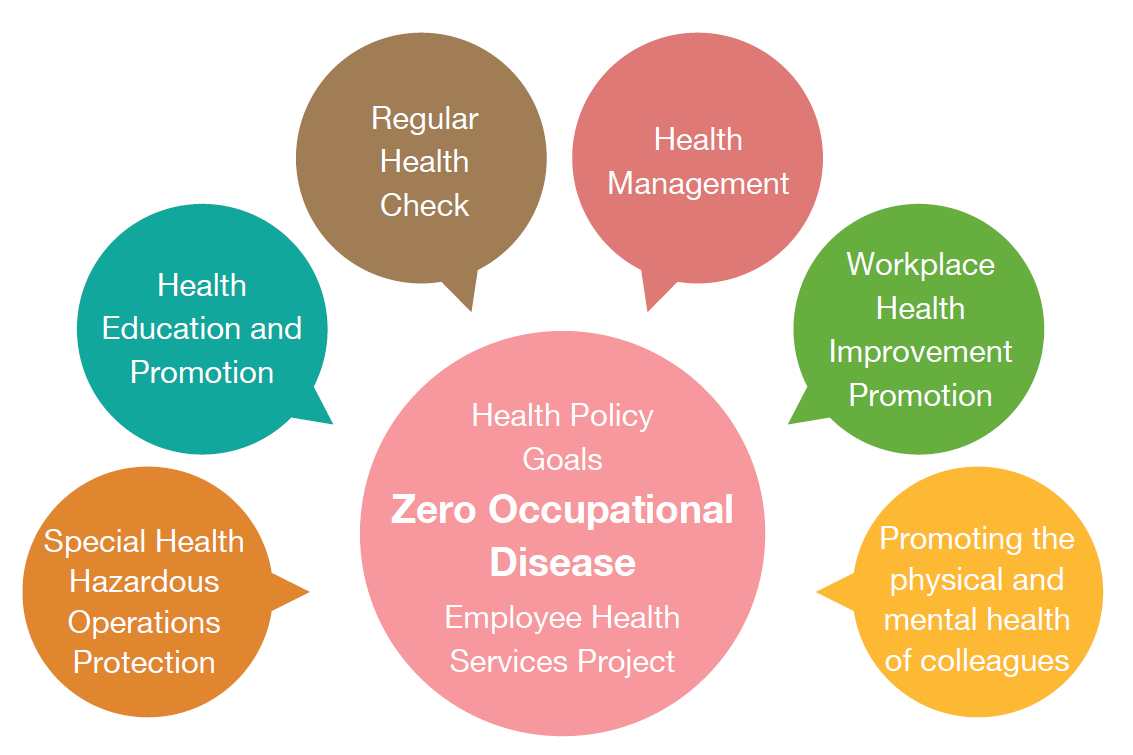
Health Promotion
TIPC plans annual health check-ups, management, and promotion activities for its employees. It formulates an Employee Health Service Plan and implements five major health protection plans, including those for human factors, illegal acts, excessive workloads, workplace maternity, and middle-aged and elderly workers. The company also employs dedicated occupational health nurses to conduct regular or periodic health assessments, health management, and tracking for employees. Specialized occupational medicine physicians and on-site health service doctors from medical institutions are engaged to provide on-site health consultation services to employees. Additionally, the company has established the Occupational Safety and Health Management Regulation for Contractors to ensure that contractors employ insured workers and implement health check-ups (physical examinations or on-the-job health examinations). Access control data is recorded and monitored for the implementation of health management and health promotion. In 2023, there were no occupational disease incidents among the company's employees and non-employee workers (contractors) (Note: Occupational diseases are defined according to the Labor Health Protection Regulations).
- Health Check-ups and Health Consultation:
To take care of the employees of TIPC, regular general health check-ups and special operation health check-ups (for noise, dust, abnormal air pressure, and long-term night shifts) are conducted annually, surpassing regulatory requirements. Based on the health check-up report results, dedicated occupational health service physicians are arranged to provide 1-on-1 consultation and health tracking services, as well as care. The service employee health checks was 98.1%, with 1,071 individuals participating out of 1,092 scheduled individuals. Those who did not participate were adjusted to the next year's implementation due to personal reasons.
Employee Health Check-up Statistics and Costs | ||
---|---|---|
Examination Items | General Health Check-up Items | Special Health Check-up Items |
Conducted in accordance with the Labor Health Protection Regulations | Noise, Dust, Abnormal Air Pressure, etc. | |
Number of people inspected (people) | 1,071 | 34 |
Inspection fee (NT$ thousands) | 4,819.5 | 25.76 |
- The company designs various health promotion programs annually targeting different potential health issues among employees, such as obesity, aging, and sedentary lifestyles. These programs include activities like leadership summit challenge, employee expeditions to Yushan, weight loss courses, vegetarian lifestyle dietary courses, aerobic exercises, gym experiences, and mountain climbing training.
.jpg)
Workplace Diversity Health Promotion Series Healthiest Eating: DIY Low-Carb (Healthy) Menu Workshop
.jpg)
Mindfulness Art Therapy
.jpg)
Mount Guanyin Hiking Activity
.jpg)
Supervisor Summit Challenge
.jpg)
Supervisor Summit Challenge Employee Expedition to Yushan
.jpg)
JS Jazz Sculpture Course